12 Stress Transformation
Introduction
Click to expand
In the preceding chapters, we have discussed how to find normal stress and shear stress due to various loading situations. We have also seen how those stresses can vary depending on the location of the point on the body in question. The combination of normal stress and shear stress that exists at a point is referred to as the general stress state. When we restrict analysis to 2D states of stress, we can represent the stress state on a 2D stress element as discussed in Section 4.7 and illustrated in Figure 4.7 for the xy plane.
The plane of the stress state is based on the coordinate system chosen for calculating the stresses. The coordinate system is most often chosen based on what is considered to be the most straight forward system for the given loading directions and geometrical orientation of the body. However, the plane for which the stresses are most easily calculated is not always the only plane for which we we would want to know the stress state.
For example, Figure 12.1 shows an air duct which is part of a heat pump system and is subject to internal air pressure. The welded seams are wound in a helical pattern that forms an angle with the horizontal axis. In Chapter 13, simple equations to calculate stress in the xy-plane due to pressure are developed. However, in this case, it is additionally important to know the stresses in the directions parallel and perpendicular to the weld seams (the x’y’ plane) to ensure that the joint could tolerate the loading. It would be useful to be able to transform the stresses we can most easily calculate in x and y directions to the x’ and y’ directions.
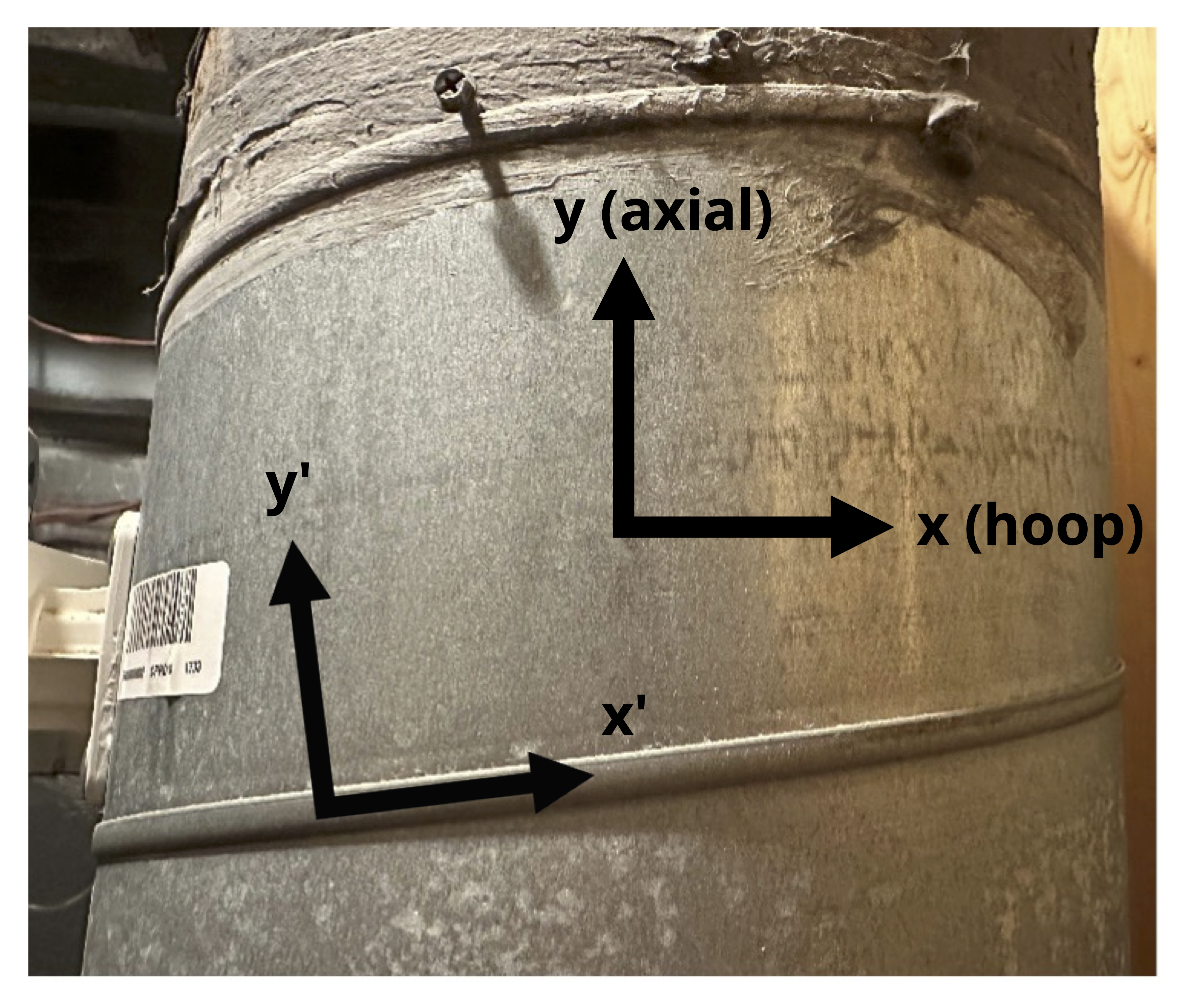
In this chapter, we will start by discussing in more detail how to represent a 2D stress state on a stress element (Section 12.1).
Then we will derive stress transformation equations that allow us to use a given stress state in one plane to find the corresponding stress state in different planes (Section 12.2). This process is known as stress transformation.
We will also derive equations that allow us to determine the planes on which the maximum and minimum normal and shear stresses occur and the corresponding stress states (Section 12.3). The maximum and minimum normal stresses are known as principal stresses.
In Section 12.4, we will discuss an alternative graphical method for performing stress transformation, known as Mohr’s circle.
In Section 12.5, we will use Mohr’s circle to expand our analysis and look at the stresses not only in the original 2D plane, but also at the out-of-plane stresses.
Click to expand
12.1 Stress Elements for 2D Stress States
A square stress element shows the normal stress and shear stress at a point for a 2D stress state. Here we will discuss the important aspects of the stress element:
1) Plane of the element:
The coordinate axes on the stress element represent the plane on the body where the point is located, with the positive directions indicated by arrows and axes labels. To determine the plane a point is on, one needs to observe the axes on a square element on the side of the body when viewing it straight on. Figure 12.2 illustrates 3 points on a body, each on a different plane (xy, yz, and xz).
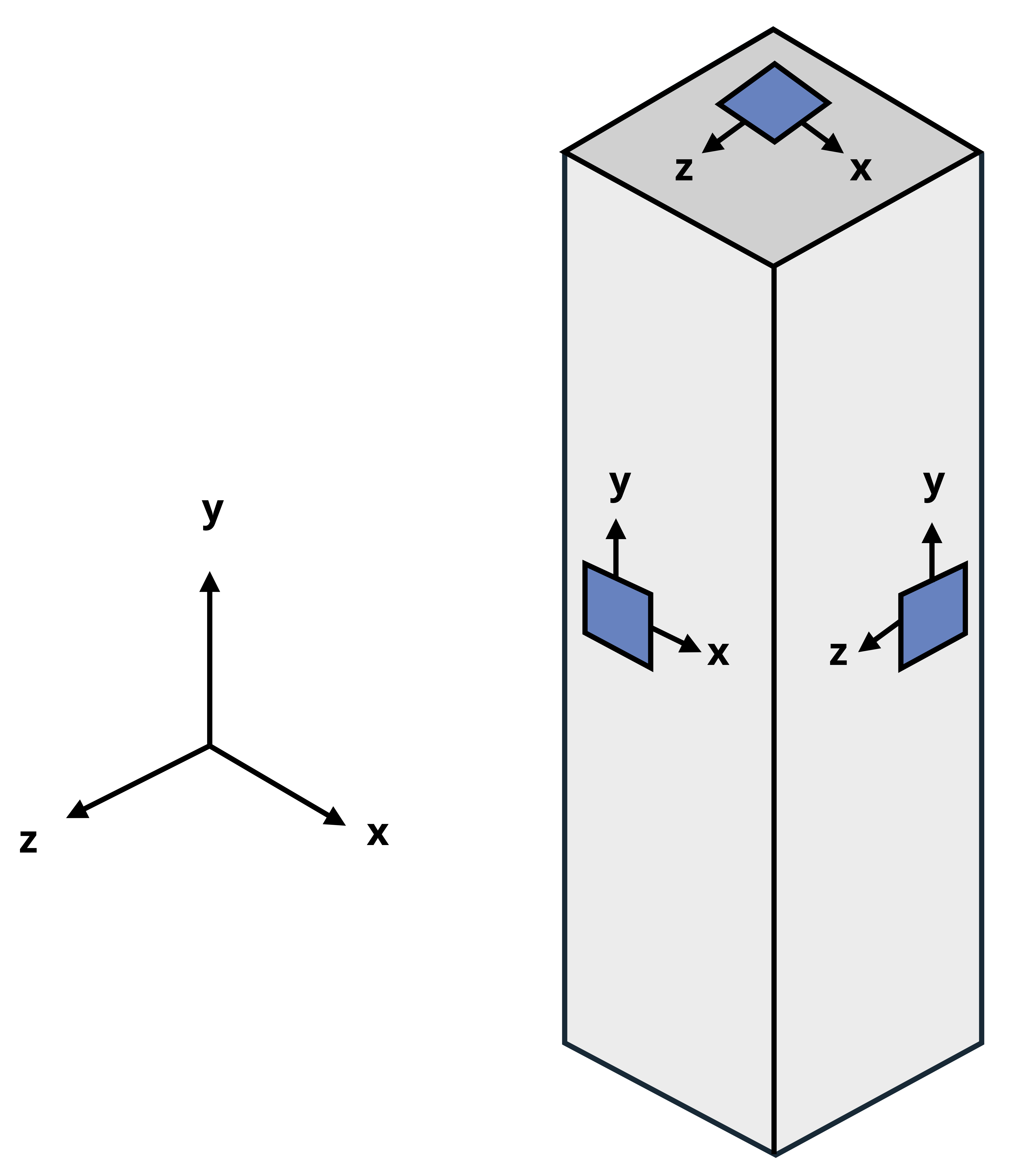
2) Positive and negative faces
We refer to the edges of the element as positive faces and negative faces depending on which way the coordinate axes are oriented. For example, if the vertical coordinate axis is positive upwards, then the top edge of element is the positive face for that coordinate axis and the bottom edge is the negative face. This is illustrated for two different planes in Figure 12.3.
3) Normal stresses
Normal stresses that are positive (tensile) are illustrated by arrows that point away from the element. Negative normal stresses (compressive) point towards the element. Normal stresses directed in the horizontal direction are shown on the left/right edges of the element and normal stresses directed in the vertical direction are shown on the top/bottom edges.
4) Shear stress
As explained in Section 4.7, the shear stress will be the same on all sides of the stress element. The manner in which the shear stress arrows are oriented around the body indicate the sign. A positive shear stress is one for which the shear stress arrow goes in a positive direction on a positive face or in a negative direction on a negative face. No matter which face you choose to examine, you should reach the same conclusion. The magnitude of the shear stress is usually specified in one corner of the element.
For example, in Figure 12.3, we can see that for the positive shear stress example, the shear stress arrow on the +x-face goes in the + y direction and the shear stress arrow on the -(x-face) goes in the -y direction. Either way, a positive shear stress is indicated and we would get the same result examining the y-faces.
For the negative shear stress example, the shear stress arrow on the +x-face goes in the -z direction and the shear stress arrow on the -(x-face) goes in the +z direction. Either way, a negative shear stress is indicated and we would get the same result examining the z-faces.
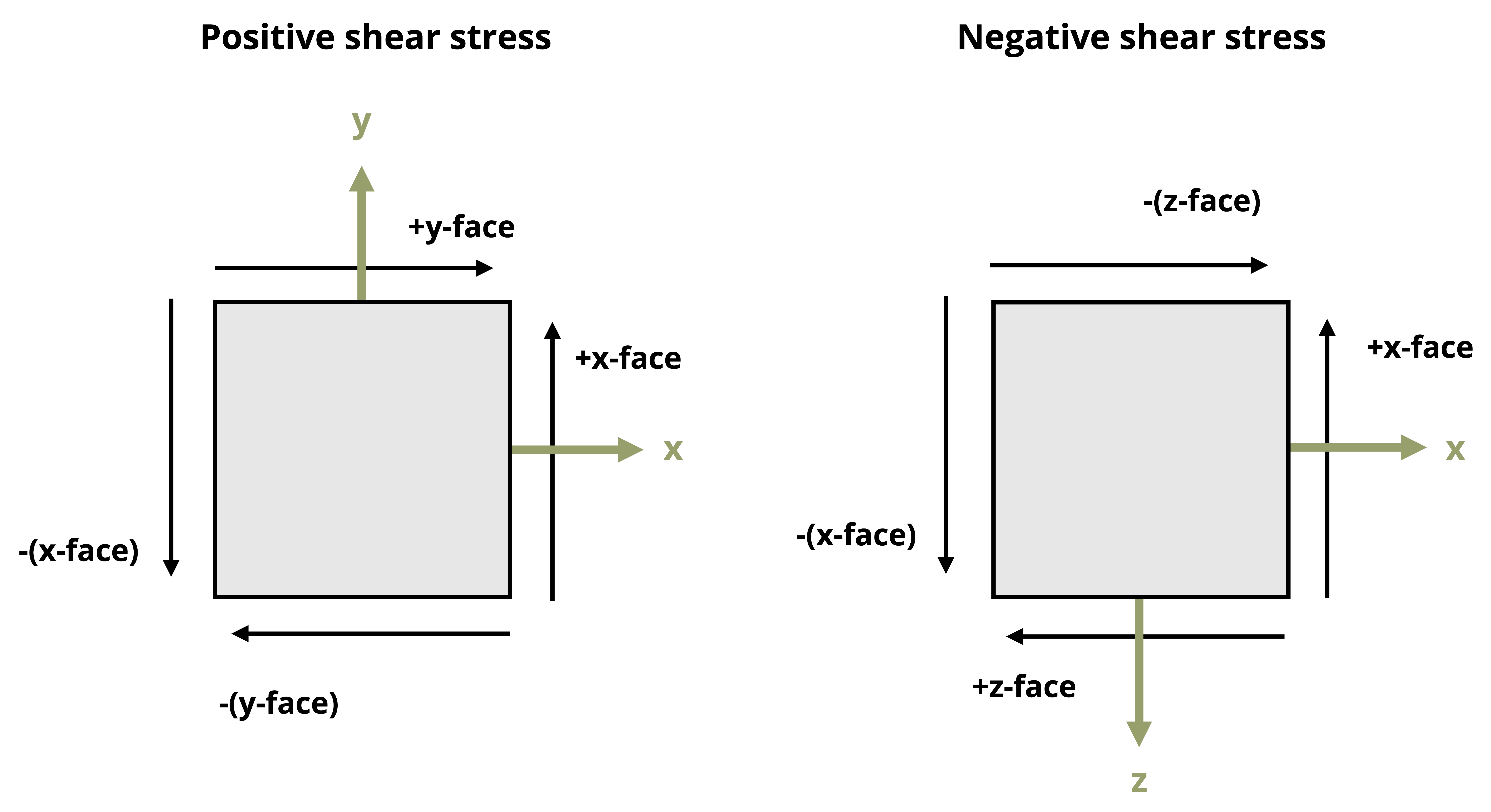
An example of a fully drawn stress element can be found in Figure 12.4. In this case the shear stress is 𝜏xz = +16 MPa (note the positive z directed shear stress arrow on the positive x-face), and the normal stresses are 𝜎x = -150 MPa and 𝜎z = +90 Mpa.
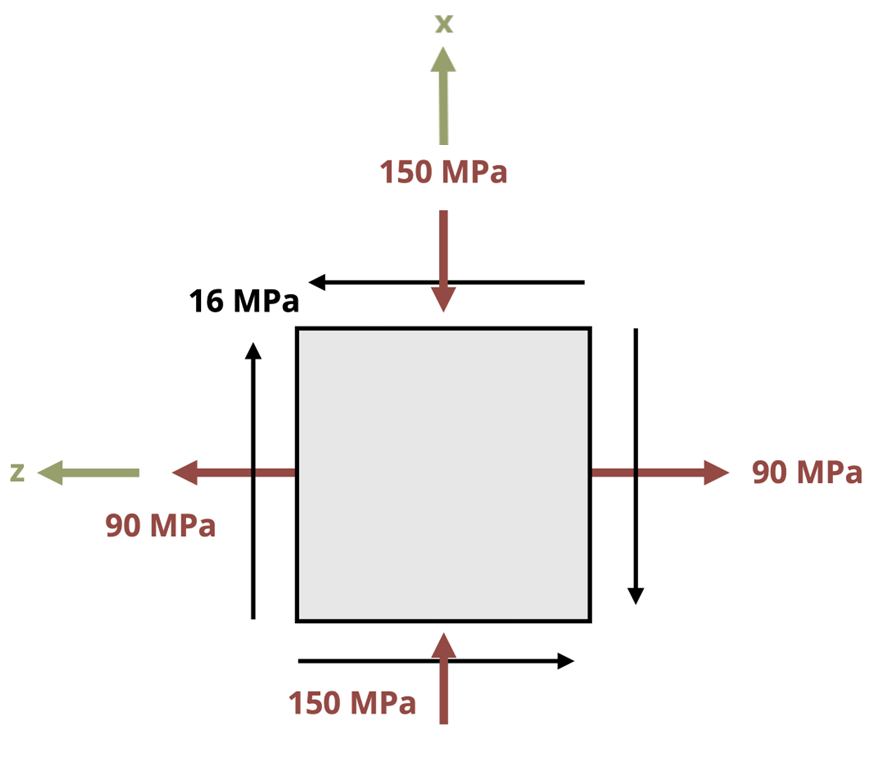
12.2 Stress Transformation Equations
Click to expand
In section Section 12.2.1, stress transformation equations are derived that allow us to use a set of stresses in one given plane (for example σx, σy, and τxy) as inputs to determine stresses in any other plane of interest. Understanding the derivations will help lend clarity to the inputs and outputs of the equations. If you wish to skip the derivations, you can simply jump ahead to the results, Equation 12.1 and/or Equation 12.2, which are boxed in below to make them easier to find. Section 12.2.1 covers the details of how to use the equations.
12.2.1 Derivation of Equations
Transformation of a uni-axial stress state was already examined in Section 2.4. In that case, we took a known force acting in the axial direction and determined the stress on an inclined plane. The current derivation for a more general stress state will be based on the same idea of cutting a section and applying equilibrium.
Figure 12.5 shows a stress element representing a general stress state in the xy-plane and the FBD (but with stresses instead of forces) of the element cut along the plane of interest. The n and t directions are normal and parallel to the incline, respectively, and 𝜃 and 𝛽 are complementary angles.
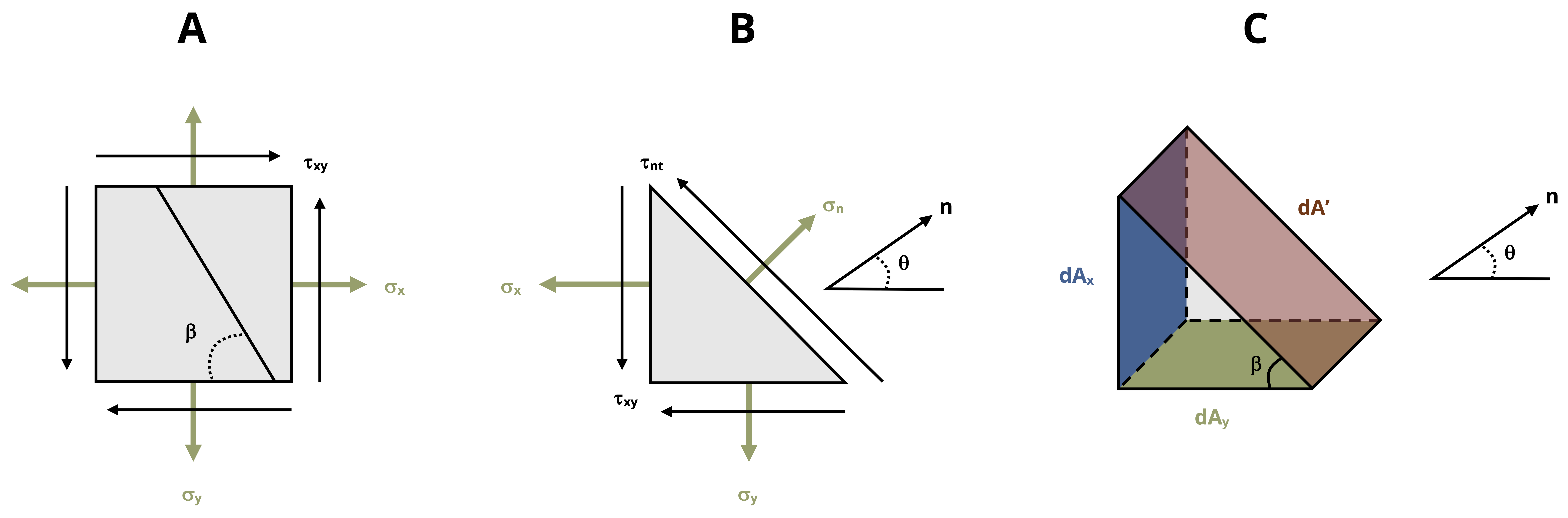
We can proceed as follows:
1) Write expressions for the forces that correspond to the stresses acting on the cut element by multiplying the stresses with the area of the side of the element they act on. These areas are illustrated in Figure 12.5 (C). We can see that σy and the τxy on the bottom face of the element act on area dAy, while σx and the τxy on the left face of the element act on area dAx.The internal forces normal and parallel to the incline act on area dA’.
On the left face, we have:
\[ F_x=-\sigma_x\ dA_x\\ F_y=-\tau_{xy}\ dA_x\\ \]
On the bottom face we have:
\[ F_y=-\sigma_y\ dA_y\\ F_x=-\tau_{xy}\ dA_y\\ \]
where the negative signs for both faces are because the stresses act to the left (negative x) and down (negative y).
On the inclined face we have:
\[ \begin{aligned} &F_x=\sigma_n\ dA'\ cos(\theta)-\tau_{nt}\ dA' sin(\theta)\\ &F_y=\sigma_n\ dA'\ sin(\theta)+\tau_{nt}\ dA' cos(\theta)\\ \end{aligned} \]
2) Express dAx and dAy in terms of dA’. Based on trigonometry, we have:
\[ \begin{aligned} dA_x & =dA'\sin(\beta)\\ &=d A^{\prime} \cos (\theta)\\ \end{aligned} \]
\[ \begin{aligned}dA_y & =dA'\cos(\beta)\\&=d A^{\prime} \sin (\theta)\\\end{aligned} \]
3) Substitute these area expressions into the force equations and write the force equilibrium equations:
\[ \begin{gathered}\sum F_x=-\sigma_x\ d A^{\prime} \cos (\theta)-\tau_{xy}\ d A^{\prime} \sin (\theta)+\sigma_n\ dA' cos(\theta) -\tau_{n t}\ d A^{\prime} \sin (\theta)=0 \\[10pt]\sum F_y=-\tau_{xy}\ d A^{\prime} \cos (\theta)-\sigma_y\ d A^{\prime} \sin (\theta) +\sigma_n\ dA' sin(\theta)+\tau_{n t}\ dA'\ cos(\theta)=0\end{gathered} \]
4) Solve the equilibrium equations for σn and τnt and simplify:
\[ \boxed{\begin{aligned} & \sigma_n=\sigma_x \cos ^2(\theta)+\sigma_y \sin ^2(\theta)+2 \tau_{x y} \sin (\theta) \cos (\theta) \\[10pt] & \tau_{n t}=-\left(\sigma_x-\sigma_y\right) \cos (\theta) \sin (\theta)+\tau_{x y}\left(\cos ^2(\theta)-\sin ^2(\theta)\right) \end{aligned}} \tag{12.1}\]
These equations are known as the stress transformation equations.
Alternatively, implementing the trigonometric identities:
\[ \begin{gathered} \cos ^2(\theta)=\frac{1+\cos (2 \theta)}{2} \\ \sin ^2(\theta)=\frac{1-\cos (2 \theta)}{2} \\ \sin (2 \theta)=2 \sin (\theta) \cos (\theta) \\ \cos (2 \theta)=\cos ^2(\theta)-\sin ^2(\theta) \end{gathered} \]
The transformation equations can also be expressed as:
\[ \boxed{\begin{aligned} \sigma_n & =\frac{\sigma_x+\sigma_y}{2}+\frac{\sigma_x-\sigma_y}{2} \cos (2 \theta)+\tau_{x y} \sin (2 \theta) \\[10pt] \tau_{n t} & =-\frac{\sigma_x-\sigma_y}{2} \sin (2 \theta)+\tau_{x y} \cos (2 \theta) \end{aligned}} \tag{12.2}\]
𝜎n = Average normal stress perpendicular to the inclined plane [Pa, psi]
𝜏nt = Average shear stress parallel to the inclined plane [Pa, psi]
𝜎x = Average normal stress in the x-direction, prior to any transformation [Pa, psi]
𝜎y = Average normal stress in the y-direction, prior to any transformation [Pa, psi]
𝜏xy = Average shear stress in the xy plane, prior to any transformation [Pa, psi]
𝜃 = Angle between x-axis and transformed stress being caculated [\(^\circ\), rad]
Either Equation 12.1 or Equation 12.2 will work. The choice over which set to use is based on personal preference.
12.2.2 Using the Stress Transformation Equations
While the n and t directions have been used to refer to the directions normal and parallel to an incline, a planar element will have two normal directions, as represented by x’, y’ in Figure 12.6. We can distinguish between the two normal stresses by the angle that is used in the stress transformation equation for 𝜎n. Based on how 𝛳 was defined in the derivation of the transformation equations, we can say:
\[ \sigma_{x'}=\sigma_n(\theta)\\ \sigma_{y'}=\sigma_n(\theta+90^\circ)\\ \tau_{x' y'}=\tau_{nt}(\theta) \]
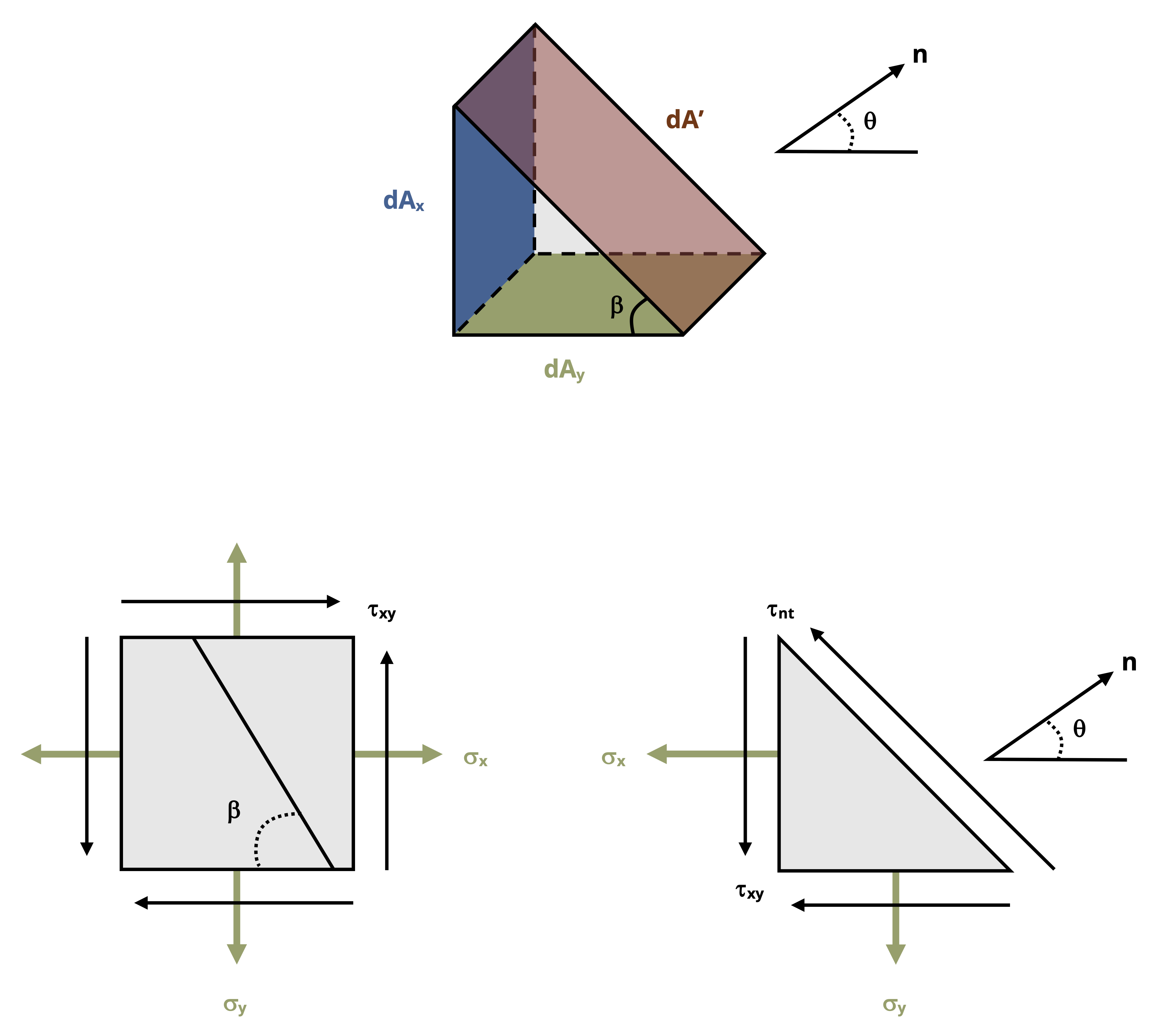
Another way to quickly determine σy’ once σx’ is known is to use the concept of stress invariance, which says that the sum of the normal stresses remains constant across different planes:
\[ (\sigma_x\ +\sigma_y)=constant \]
or:
\[ \boxed{(\sigma_{x'}\ +\sigma_{y'})=(\sigma_x\ +\sigma_y)} \tag{12.3}\]
It is imperative that one understands which angle to substitute into the transformation equations given above, including whether it is positive or negative. To ensure the correct angle and sign is used, refer to Figure 12.7 and take the following steps:
Draw a line that represents one side of the plane of interest
Draw the x-axis (positive to the right)
Draw the axis normal to the plane of interest. It does not matter if you draw the normal axis oriented counterclockwise or clockwise from the x-axis as long as you use the correct sign for θ (see step 4).
Determine the angle that goes from the x-axis to the normal axis. This angle is θ. If the direction from the x-axis to the normal axis is counterclockwise, then θ is positive. If the direction from the x-axis to the normal axis is clockwise, then θ is negative.
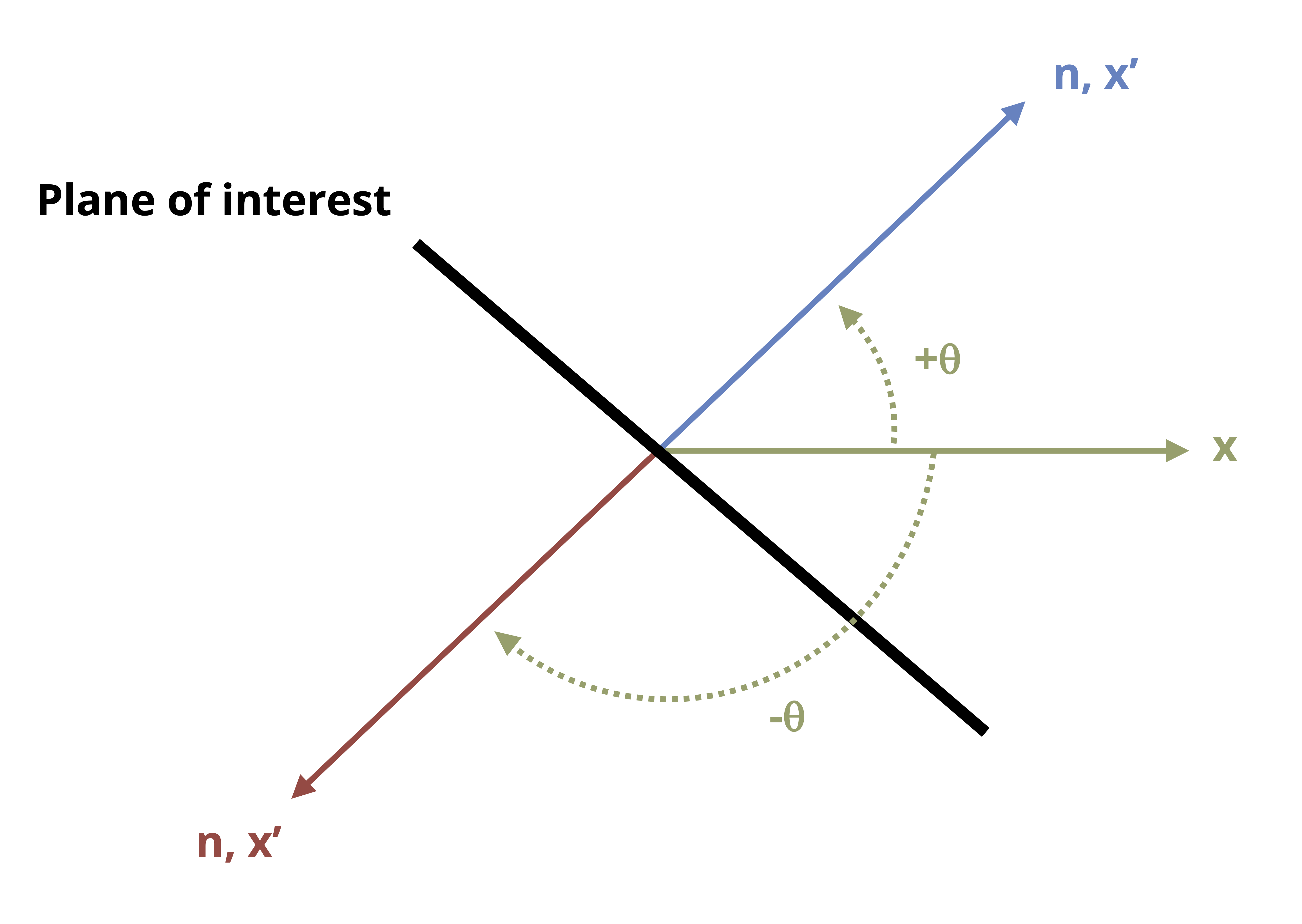
In some cases, the reference stress state may not be in the xy plane, or the x and y axes may be oriented differently from the orientation in Figure 12.5. In these cases, some adjustments will need to be made in implementing the transformation equations to ensure consistency of inputs with how the equations were derived.
As an example, consider the reference stress state in Figure 12.8. As given, you might question which stress to substitute in for 𝜎x and which to substitute for 𝜎y. Keeping in mind that the transformation equations were derived based on a coordinate system in which the the horizontal axis is positive to the right and the vertical axis is positive upwards, we can ensure consistency with the inputs if we re-orient the reference stress element in the same way, as is also shown in the Figure 12.8. We can then attribute the coordinate designated to the horizontal direction to correspond to the x terms in the transformation equations and the coordinate designated to the vertical direction to correspond to the y terms in the transformation equations. In the case of the stress state in Figure 12.8, we would substitute -150 MPa for 𝜎x, 90 MPa for 𝜎y, and 16 MPa for τxy.
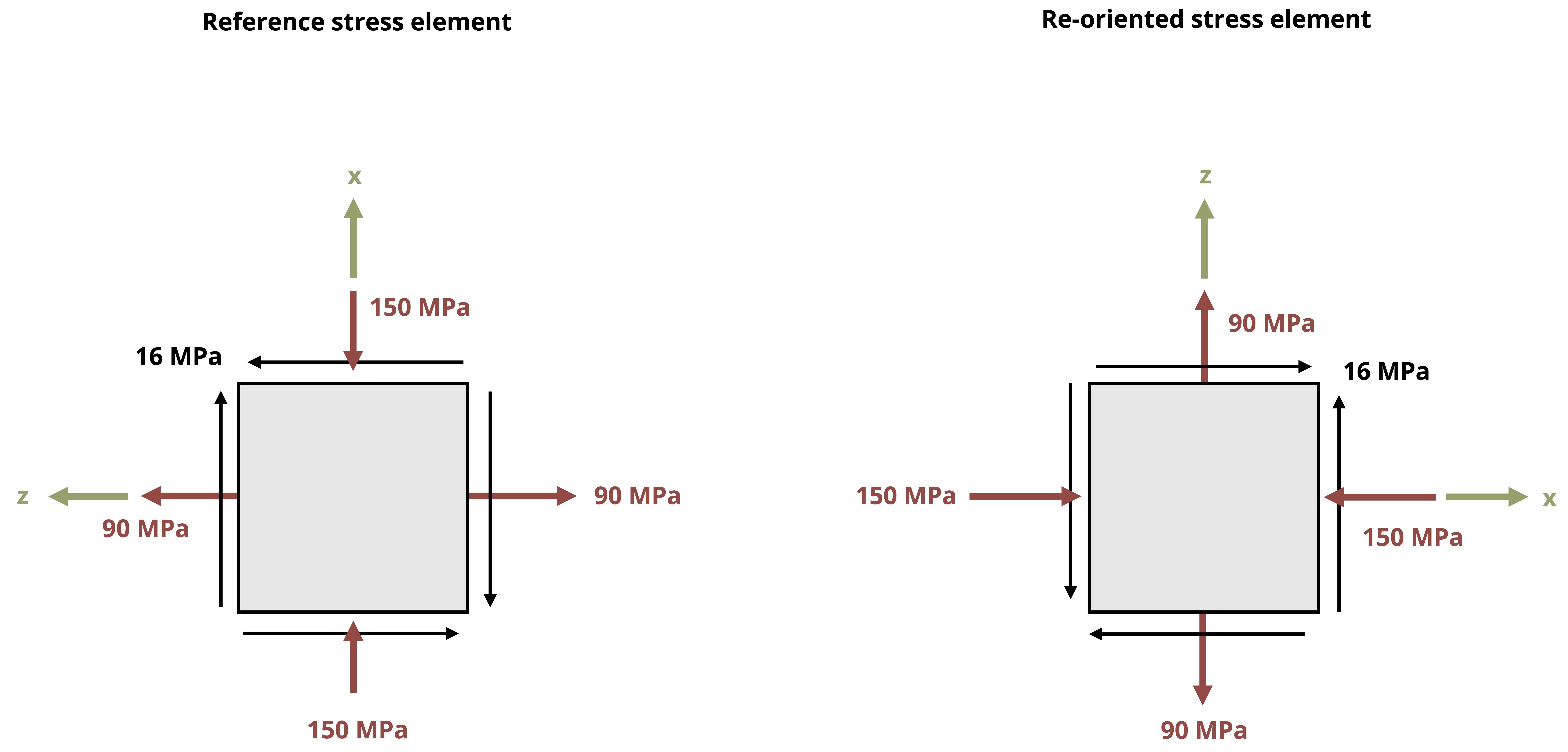
Example 12.1 and Example 12.2 below illustrate the use of the stress of transformation equations.
12.3 Principal Stresses and Max/Min Shear Stress
Click to expand
Often, the plane we are the most concerned with is the one on which the normal stress or the shear stress is at a maximum because that is the one on which failure is most likely occur. The maximum and minimum normal stresses are referred to as the principal stresses (σ1 and σ2) and the planes on which they act (described by angle of rotation of the stress element, θp1 and θp2) are the principal planes. The maximum and minimum shear stresses are simply referred to as the maximum and minimum shear stress, respectively, and the planes on which they occur are referred to simply as the planes of maximum and minimum shear stress (denoted as θs1 and θs2).
It is important to note that in this section, only rotations within a two dimensional plane are being considered. As will be seen in Section 12.5, the principal planes and principal stresses are the same even when considering out of plane rotation of the stress element (see Figure 12.9), but the max shear stress could be different. Therefore, the max and min sheer stress as determined by the below derived equations will be referred to as the max/min in-plane shear stress.
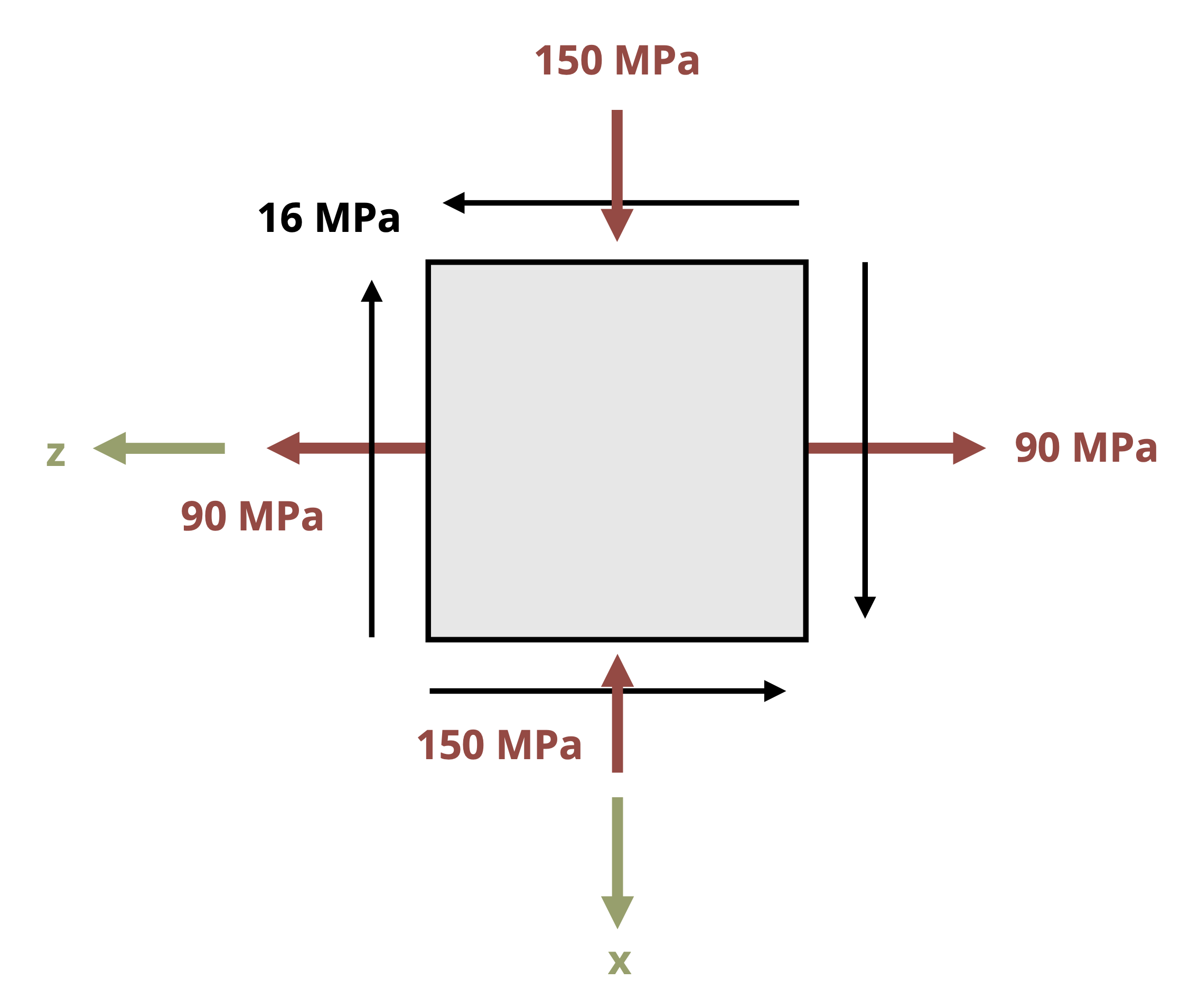
As we rotate the stress element and the angle θ changes, the stress changes in a predictable way. Figure 12.10 shows the variation of normal stress σx’ with angle θ. The principal stresses can be seen to occur at specific values of θ. These angles will be 90° apart from one another. A similar graph could be drawn for τx’y’.
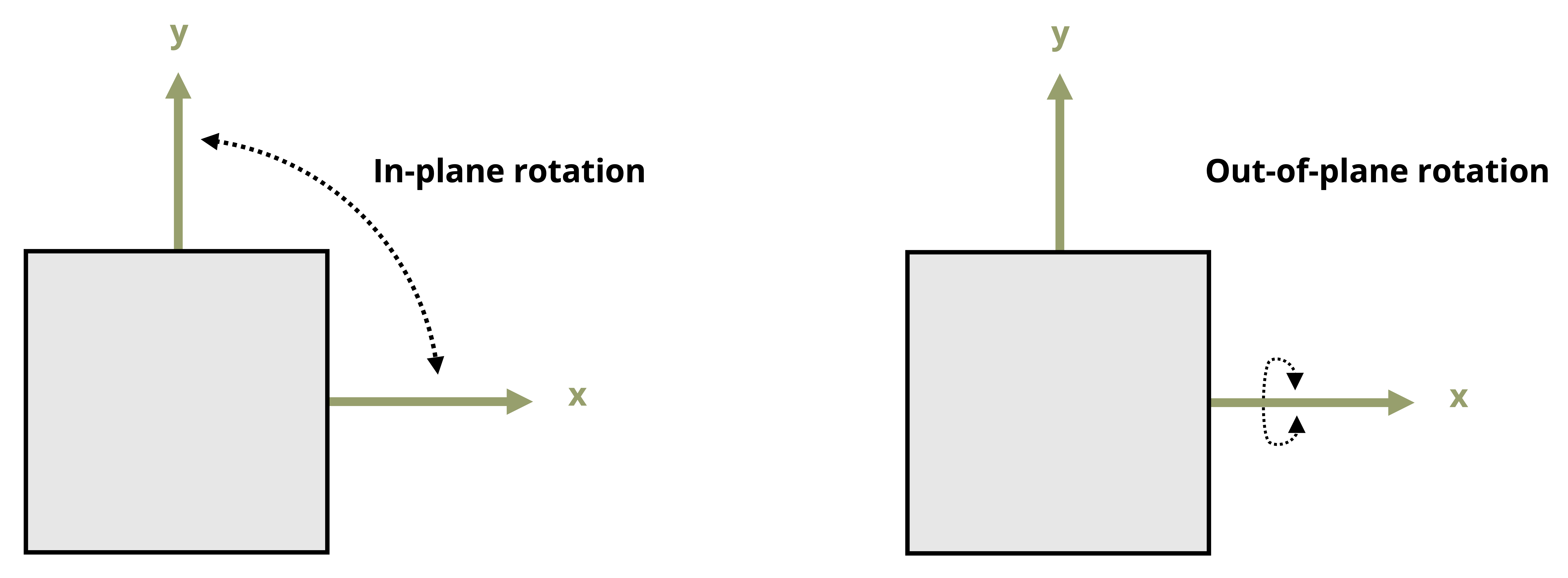
Since these stresses are maximums and minimums (i.e., the slope of the curve is zero at these points) and since the transformation equations derived in Section 12.2.1 are functions in terms of the plane rotation angle θ, we can simply take the derivatives of the two equations and set them equal to zero to find the angles at which we would get the maximum and minimum of each type of stress. Using the second set of transformation equations derived in Section 12.2.1 (though the first set would yield the same results):
\[ \begin{aligned} & \frac{d \sigma_n}{d \theta}=-\left(\sigma_x-\sigma_y\right) \sin \left(2 \theta_p\right)+2 \tau_{x y} \cos \left(2 \theta_p\right)=0 \\[10pt] & \frac{d \tau_{n t}}{d \theta}=-\left(\sigma_x-\sigma_y\right) \cos \left(2 \theta_s\right)-2 \tau_{x y} \sin \left(2 \theta_s\right)=0 \end{aligned} \]
Notice that θ is subscripted with a p in the first equation since this angle represents a principal plane as defined above. Similarly, θ is subscripted with an S in the second equation since this angle represents a plane of max or min in-plane shear stress.
These equations can be rearranged to isolate tan (2θ) on one side and subsequently used to find θp and θs values:
\[ \boxed{\begin{aligned} \tan \left(2 \theta_p\right) & =\frac{2 \tau_{x y}}{\left(\sigma_x-\sigma_y\right)} \\[10pt] \tan \left(2 \theta_s\right) & =-\frac{\left(\sigma_x-\sigma_y\right)}{2 \tau_{x y}} \end{aligned}} \tag{12.4}\]
𝜃p = Orientation of one of the principal planes, with respect to the x-axis [\(^\circ\), rad]
𝜃s = Orientation of one of the maximum shear planes, with respect to the x-axis [\(^\circ\), rad]
𝜏xy = Average shear stress in the xy plane, prior to any transformation [Pa, psi]
𝜎x = Average normal stress in the x-direction, prior to any transformation [Pa, psi]
𝜎y = Average normal stress in the y-direction, prior to any transformation [Pa, psi]
Once the angles associated with the planes of extreme stresses are determined, they can be substituted into Equation 12.1 or Equation 12.2 along with the stresses in the given plane to find the principal stresses and max/min shear stress.
A few calculation details that it will be helpful to remember are:
The inverse tangent function has two possible solutions. One solution would be the angle that will be reported by a calculator, and the other possible answer is the angle that is that angle plus or minus 180°. So if you use your calculator to solve the tan (2θp) equation, you would take half that to get the first principal angle and then add or subtract 90 degrees to that principal angle to get the second. The same idea applies to finding the two θs angles.
By convention, the most positive of the two principal stresses is denoted as σ1. The other principal stress is then σ2. The angle that produces that σ1 stress is θp1 and the angle that produces σ2 is θp2.
The max and min in-plane shear stresses will always turn out to be equal in magnitude by opposite in sign, or in other words, the minimum shear stress is always the negative of the maximum shear stress. As with the principal planes and stresses, one would need to substitute one of the θs angles into the shear stress transformation equation to determine which angle corresponds to the maximum in-plane shear stress and which corresponds to the minimum.
The angles of maximum and minimum shear stresses are 90° apart from each other, and 45° apart from the principal directions. If one principal direction is found to be, for example, 40° then the other principal direction can be determined as either (40° + 90° =) 130° or (40° - 90° =) -50°. The angles of maximum and minimum in-plane shear stress can then be determined as either (40° + 45° =) 95° or (40° - 45° =) - 5°. It is also acceptable to add or subtract 45° from 130° or from – 50°.
Given the variety of different of possible correct angles, we will use a convention that principal directions and angles of maximum and minimum shear stress will be calculated in the range – 90° ≤ θ ≤ + 90°.
If desired, the principal stresses and max./min. shear stresses can be calculated directly without first finding the principal directions:
\[ \boxed{\begin{gathered} \sigma_{1,2}=\frac{\sigma_x+\sigma_y}{2} \pm \sqrt{\left(\frac{\sigma_x-\sigma_y}{2}\right)^2+\tau_{x y}{ }^2} \\[10pt] \tau_{x \prime y^{\prime}}= \pm \sqrt{\left(\frac{\sigma_x-\sigma_y}{2}\right)^2+\tau_{x y}{ }^2} \end{gathered}} \tag{12.5}\]
𝜎1,2 = Principal stresses [Pa, psi]
𝜎x = Average normal stress in the x-direction, prior to any transformation [Pa, psi]
𝜎y = Average normal stress in the y-direction, prior to any transformation [Pa, psi]
𝜏xy = Average shear stress in the xy plane, prior to any transformation [Pa, psi]
Some useful conclusions that can be drawn simply by studying the principal plane and plane of max/min shear stress equations are as follows:
If the shear stress transformation equation given in Section 12.1 is set equal to 0 in order to find the plane at which shear stress is equal to 0, we would arrive at the same equation as the Tan(2θp) found above. We can then conclude that shear stress is 0 on the principal planes. It can also be said that if the shear stress is found to be 0 on any given plane, then that plane must be a principal plane.
The equation for tan (2θs) is the negative inverse of the equation for tan (2θp). This means that 2θs = 2θp ± 90° or θs = θp ± 45°. Recognizing this can allow one to calculate one set of angles more efficiently once the other is found.
If either of the θs angles are substituted into the normal stress transformation equation, the normal stress would work out to be the average stress \(\left(\frac{\sigma_x+\sigma_y}{2}\right)\). Once again, this recognition can help make determining the total stress state on the plane of max/min shear stress more efficient.
Example 12.3 demonstrates the calculation of the principal stresses, the maximum in-plane shear stress, and the orientations that these stresses occur at.
12.4 Mohr’s Circle
Click to expand
As an alternative to using equations to determine principal planes and stresses as well as max/min shear planes and stresses, one can use a graphical method known as Mohr’s Circle. This method is based on the fact that the stress transformation equations are actually parametric equations of a circle. The perimeter of the circle consists of coordinate points that correspond to normal stress on the horizontal axis and shear stress on the vertical axis. The advantage of using Mohr’s Circle is that it does not involve needing to recall equations and can be quick and efficient to use with some practice.
To illustrate the construction of Mohr’s circle, we will use the reference stress state element in Figure 12.11.
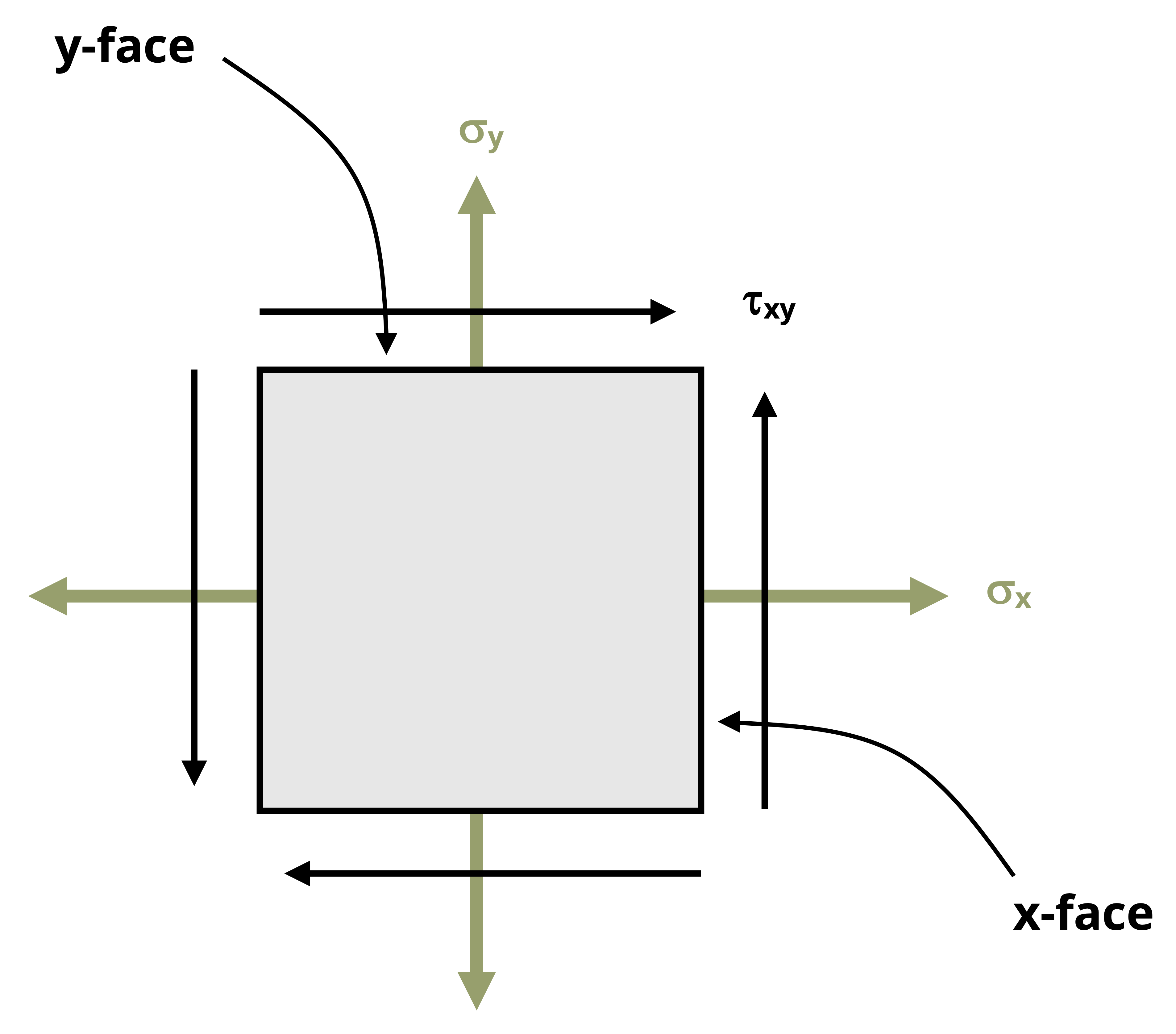
Now we can take the following steps (the fully constructed circle can be found in Figure 12.16):
To start, draw a set of coordinate axes where normal stress will be on the horizontal axis and shear stress will be on horizontal axis. Note in Figure 12.14 that the shear stress is labeled with a (CW) for clockwise on the positive side and a (CCW) for counterclockwise on the negative side. The reason is explained in step 2 below.
Plot the x-point. The x-point represents the stresses applied to the x-face of the stress element, as shown in Figure 12.12, with coordinates (𝜎x, 𝜏xy). The normal stress coordinate is positive if tensile and negative if compressive. The sign of the shear stress coordinate depends on the direction of rotation that the shear stress on the x-face will cause. If it causes the element to rotate clockwise, it is positive, and if causes the element to rotate counterclockwise, it is negative..
On the stress element in Figure 12.11, the normal stress on the x-face is tensile and the upwards shear stress tends to cause the element to rotate counterclockwise, so the x-point is (+σx, -τxy).
Figure 12.12: Stresses applied to positive x-face form the x-point. Plot the y-point. Similarly to the x-point, the y-point generally consists of coordinates (𝜎y, 𝜏xy). The sign convention is the same as for the x-point, but the sign of the shear stress coordinate depends on the rotation caused by the shear stress on the positive y-face. As illustrated in Figure 12.13 for the stress element given in Figure 12.11, the normal stress on the y face is tensile and the rightwards shear stress tends to cause the element to rotate clockwise, so the y-point is (+σy, +τxy).
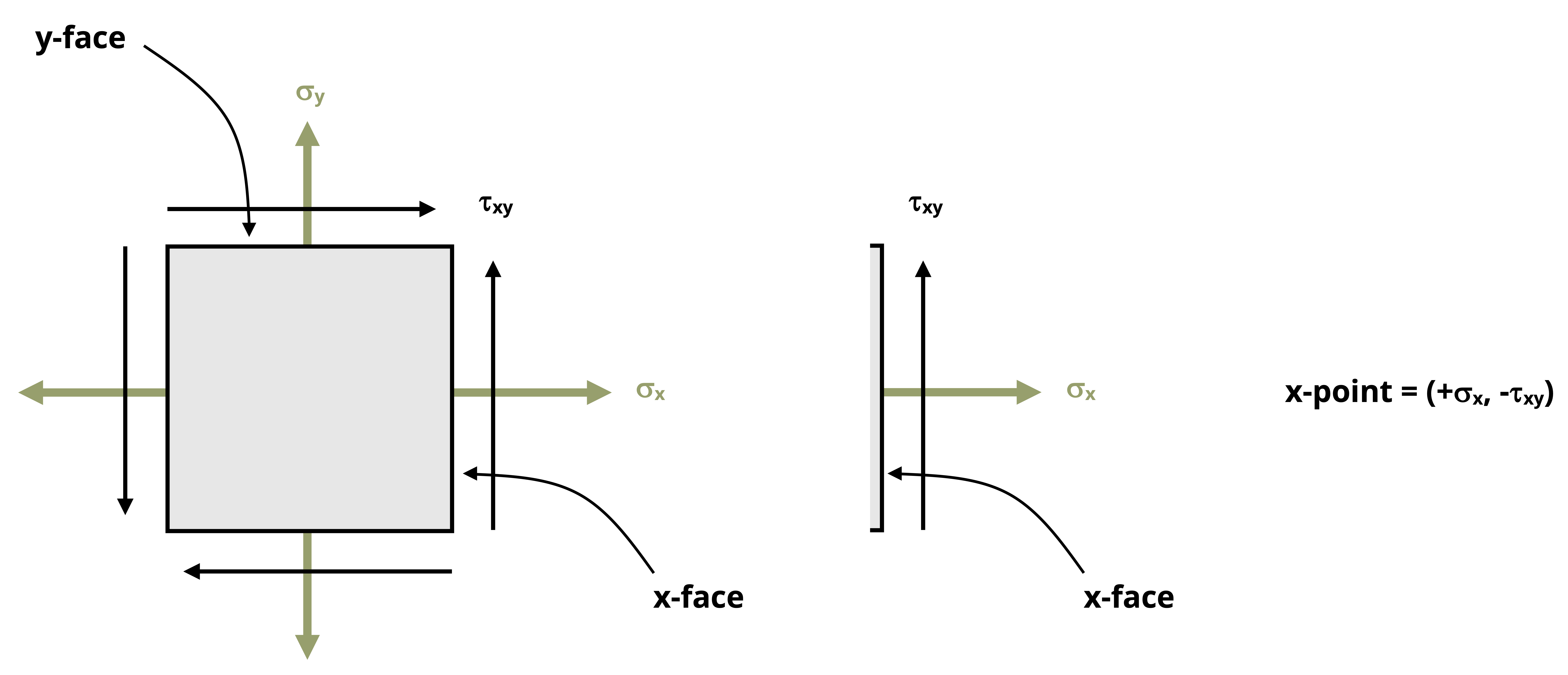
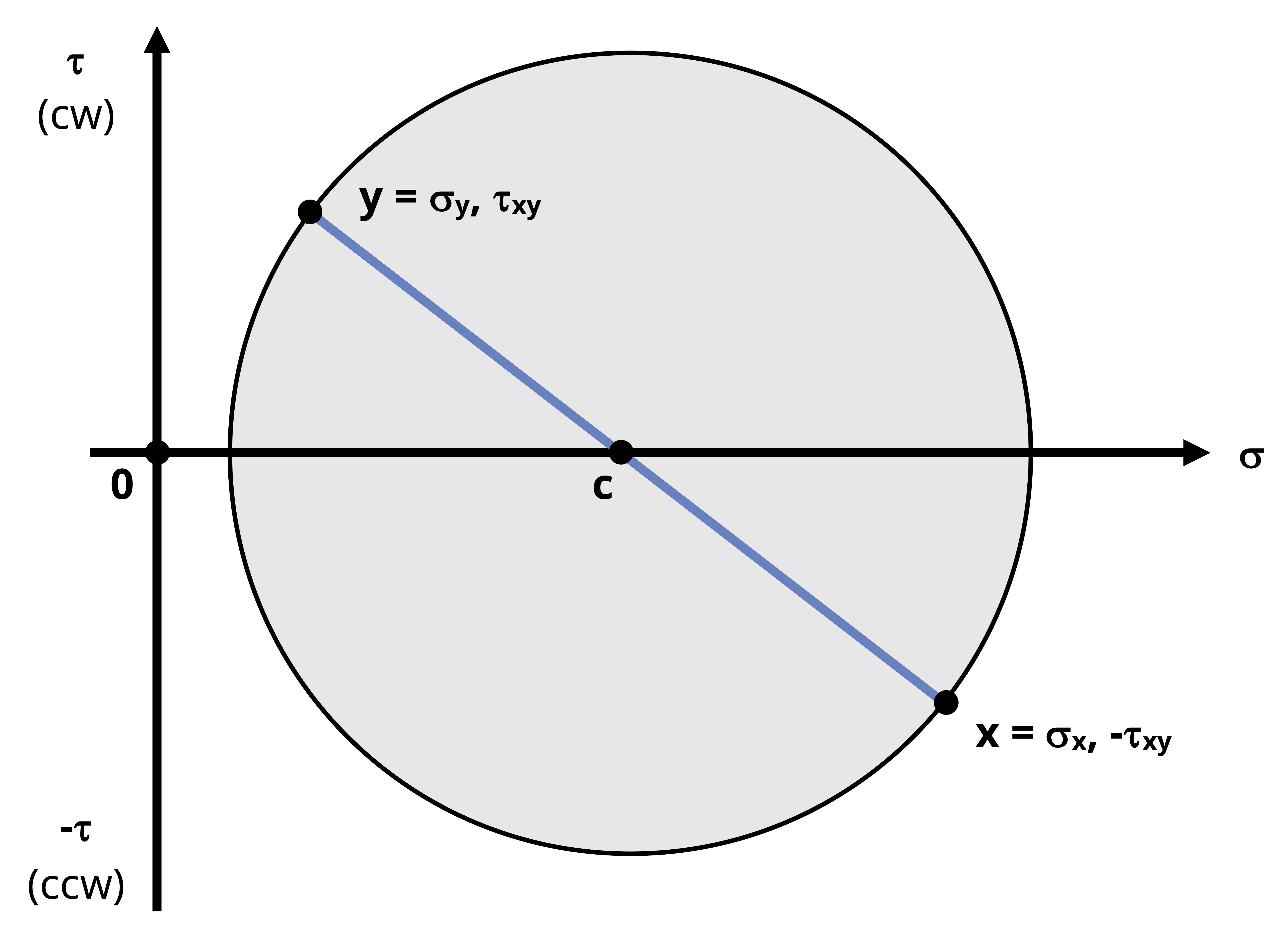
Draw the circle around the diameter formed by connecting the x- and y-points.The center of the circle is the average normal stress:
\[ C=(\frac{\sigma_x+\sigma_y}{2},0) \]
Note that use of the variable “C” below refers to the average nomal stress, \(\frac{\sigma+\sigma_y}{2}\) .
Note that the radial line that goes from C to the x-point represents the reference x-axis and the radius from C to the y-point represents the reference y-axis.
The radius, R, can be determined using of the Pythagorean Theorem on the triangle formed between C, σx, and the x-point.
\[ R=\sqrt{\left(\sigma_x-C\right)^2+\tau_{x y}^2} \]Figure 12.15 Recalling that the shear stress is zero on the principal plane, we can see that principal plane is simply the normal stress axis. Thus, we can identify σ1 to be the point on the right extreme of the circle and σ2 to be the point on the left extreme of the circle (see figure):
\[ \sigma_1=C+R\\ \sigma_2=C-R\\ \]
These points can be found on Figure 12.13.
The max and min in-plane shear stress is at the bottom and top of the circle, respectively:
\[ \tau_{max}=+R\\ \tau_{min}=-R\\ \]
The max shear stress is at the bottom because of the shear stress plotting convention discussed in steps 2 and 3.
The vertical diameter that connects 𝜏max and 𝜏min is the plane of max/min in-plane shear stress.
Since that plane passes through the center of the circle, we can confirm that the normal stress on the plane of max/min shear stress is \(\mathrm{C}=\sigma_{avg}=\frac{\sigma_x+\sigma_y}{2}\).
These points can be found on Figure 12.16.
Rotations around the circle represent twice the actual amount of rotation between planes. Furthermore, rotations counterclockwise from the x-point are positive angles and rotations clockwise from the x-point are negative angles.
Thus, the angle between the principal plane and the x-point on the circle is 2θp. This angle can be determined by applying right triangle trigonometry principles to the right triangle used to find the radius:
\[ \tan (2 \theta p)=\frac{\tau_{x y}}{\sigma_x-C} \]
Looking at Figure 12.16, we can see that in this case, the 2𝜃p angle is a counterclockwise rotation from the reference x-axis to the principal axis, so if we were to draw the stress element rotated counterclockwise to 𝜃p , 𝜎1 would be drawn on the x’ face and 𝜎2 would be drawn on the y’ face.The angle to the plane of max/min in-plane shear stress, θs, can be found in a similar manner. Visual inspection shows that 2θs will be the complement of 2θp. Recalling the convention used to apply sign to the shear stress coordinate, the angle that goes from the reference x-axis to the negative side of the shear stress axis will correspond to the rotation that results in the maximum in-plane shear stress and vice versa.
Once these quantities are known, the use of the circle to perform stress transformations at arbitrary planes requires making similar trigonometric calculations. This process is better illustrated in Example 12.4.
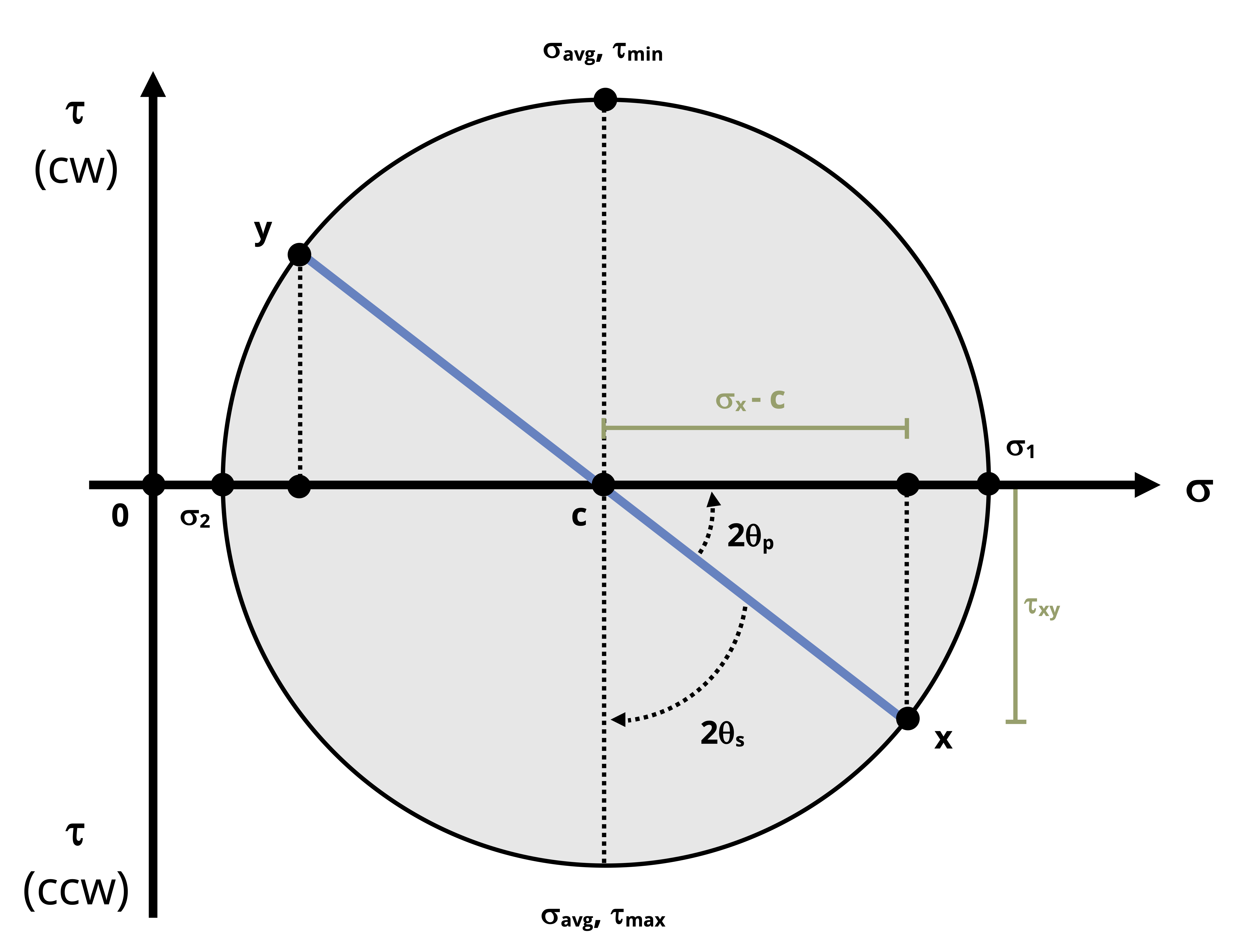
Example 12.4 demonstrates the use of Mohr’s Circle to find maximum/minimum stresses and to perform stress transformations.
12.5 Mohr’s Circle in 3-Dimensions and Absolute Max Shear Stress
Click to expand
Many materials yield or fail in shear rather than normal stress, so knowing the absolute maximum shear stress the material is subjected to is important. The methods discussed in Sections 12.2 and 12.3 provide the maximum in-plane shear stress that arises from rotations in the 2D plane (rotation around the z-axis in Figure 12.17). However, as discussed in Section 12.2, the actual maximum shear stress may result from an out of plane rotation (rotation around the x or y axes in Figure 12.17). To account for this potential circumstance, we need to evaluate a 3D stress element despite the fact that we are still restricting analysis to 2D stress states.
For the sake of this discussion, we will consider a reference stress state with stresses only in the xy plane, though it could generally be any other 2D plane. To further simplify the discussion, we will say that the stress element is already rotated around the z-axis to the principal stress state such that σx = σ1 and σy =σ2. The resulting 3D stress cube and representations of the xz and yz planes are shown in Figure 12.17. Given the plane stress restriction, 𝜏xz =𝜏yz =0, which means that the xz and yz planes are also at principal stress states. Designating the principal stress in the z direction to be σ3, we can see that the principal stresses in the xz plane are σ2 and σ3 and the principal stresses in the yz plane are σ1 and σ3. For the reference stress state (plane stress), σ3 = 0 on all planes.
As the stress cube rotates around the x-axis, σz will vary between 0 at 𝜃 =0° and σ2 at 𝜃 = 90°. Meanwhile, σy will vary in the opposite way and σx will remain unchanged. Similarly, as the stress cube rotates around the y axis, σz will vary between 0 at 𝜃 =0° and σ1 at 𝜃 = 90° while σx varies in the opposite way and σy remains unchanged.
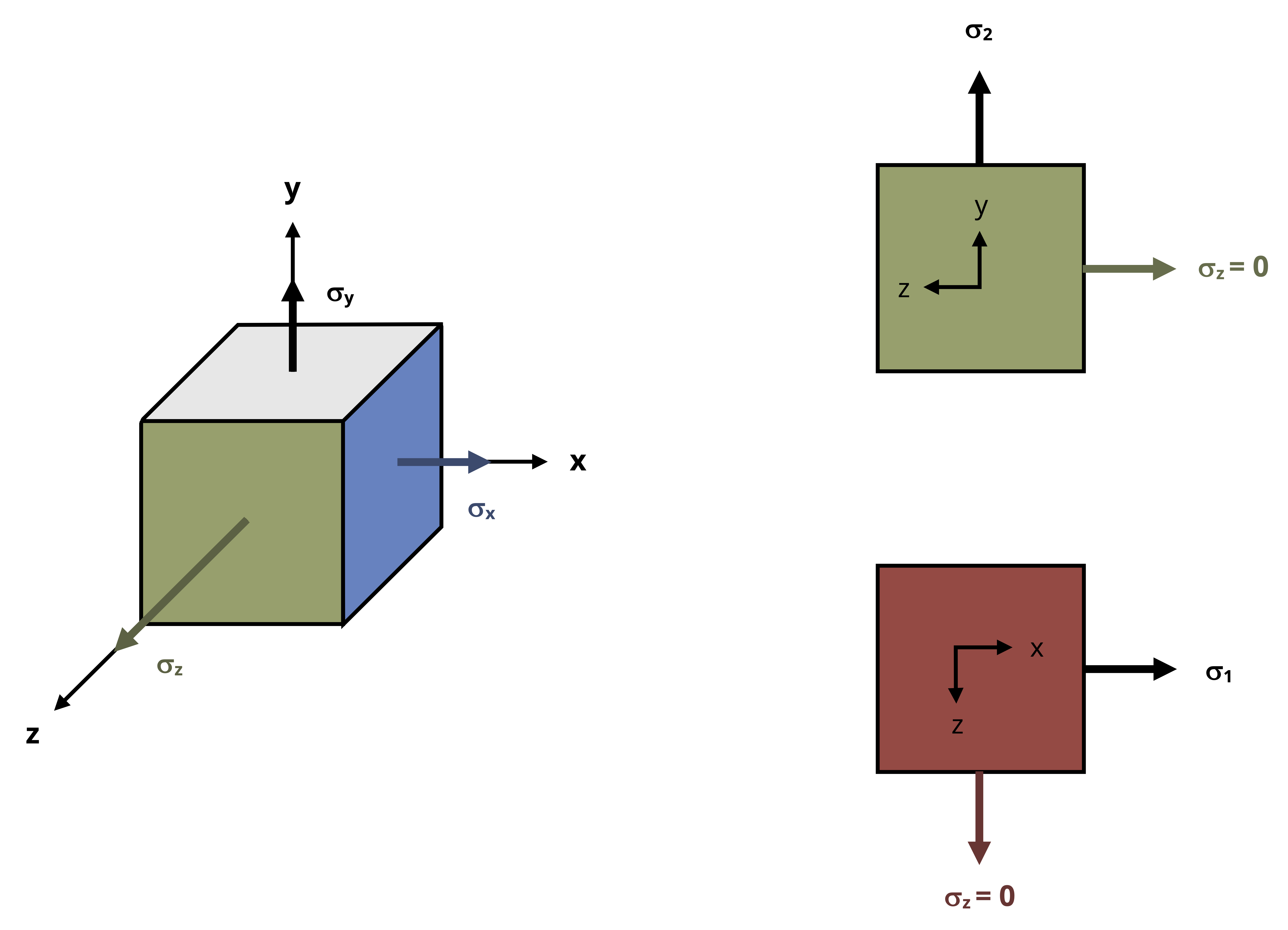
We can draw Mohr’s circle for each of the three planes in Figure 12.17 on one plot. Just as the ciricle represents rotation of the stress element around the z-axis for stresses in the xy plane, if represents rotation around the y axis for the xz plane and rotation around the x axis for the yz plane. We will consider three cases:
σ1 and σ2 are both positive
σ1 and σ2 are both negative
σ1 and σ2 have opposite signs
Case 1:
Referring to Figure 12.18, the larger inner circle is Mohr’s circle for the x-y plane as can be noted by the fact that the max and min normal stresses on that circle are σ1 and σ2, respectively. The smaller inner circle is Mohr’s circle for the y-z plane which has 0 and σ2 at the extremes. The largest circle is Mohr’s circle for the xz plane which has 0 and σ1 at the extremes. We can see in this case that the largest shear stress is given by the radius of the largest circle which is σ1/2.
So in the case that σ1 and σ2 are both positive, the absolute max shear stress is:
\[ \tau_{(\max )absolute}=\left|\frac{\sigma_1}{2}\right| \]
The absolute value is there since we know the max shear stress must be a positive shear stress given that the max and min shear stresses are negatives of each other.
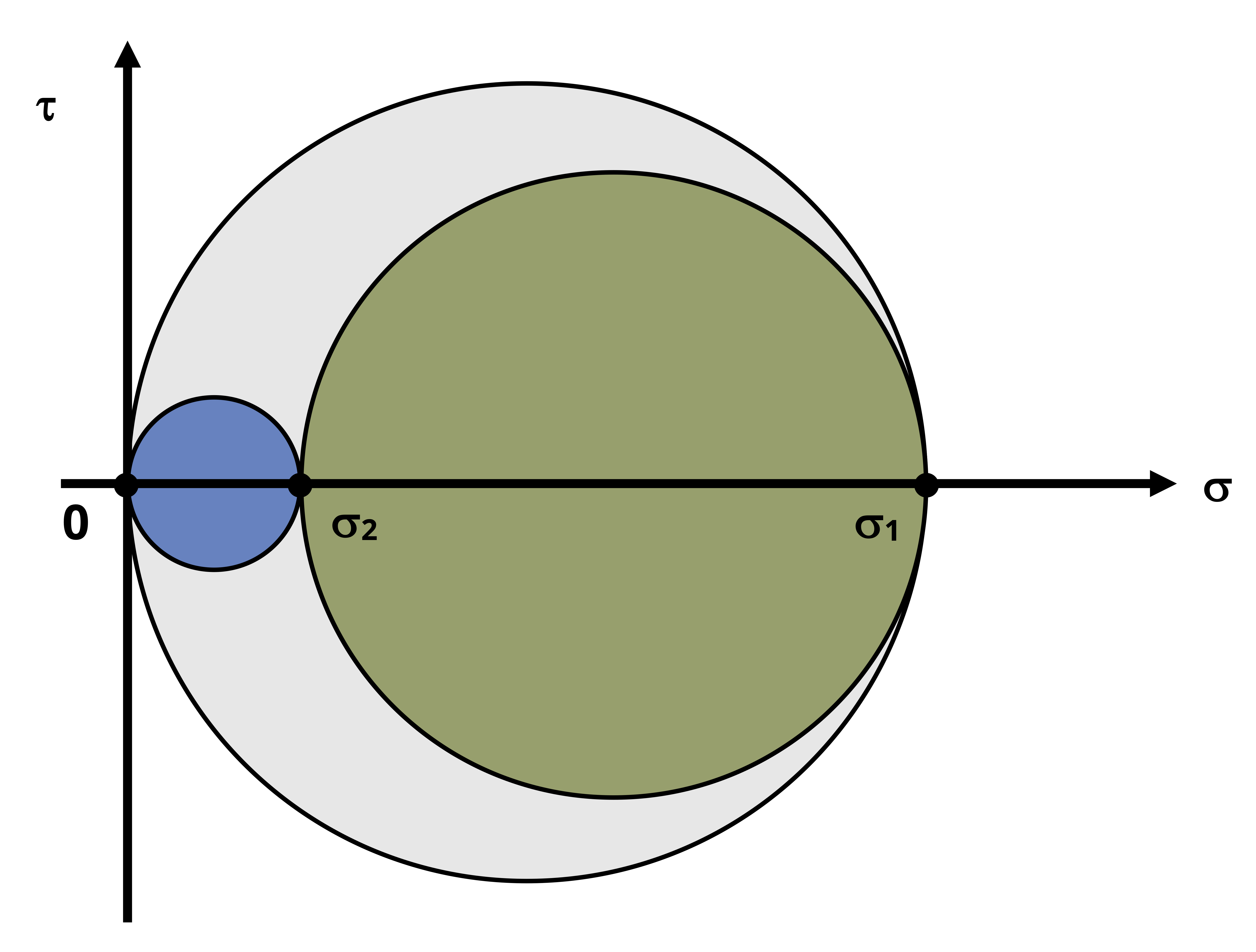
Case 2:
Referring to Figure 12.19, all the statements made in Case 1 still hold true except that the radius of the largest circle is now σ2/2.
So in the case that σ1 and σ2 are both negative, the absolute max shear stress is:
\[ \tau_{(\max )absolute}=\left|\frac{\sigma_2}{2}\right| \]
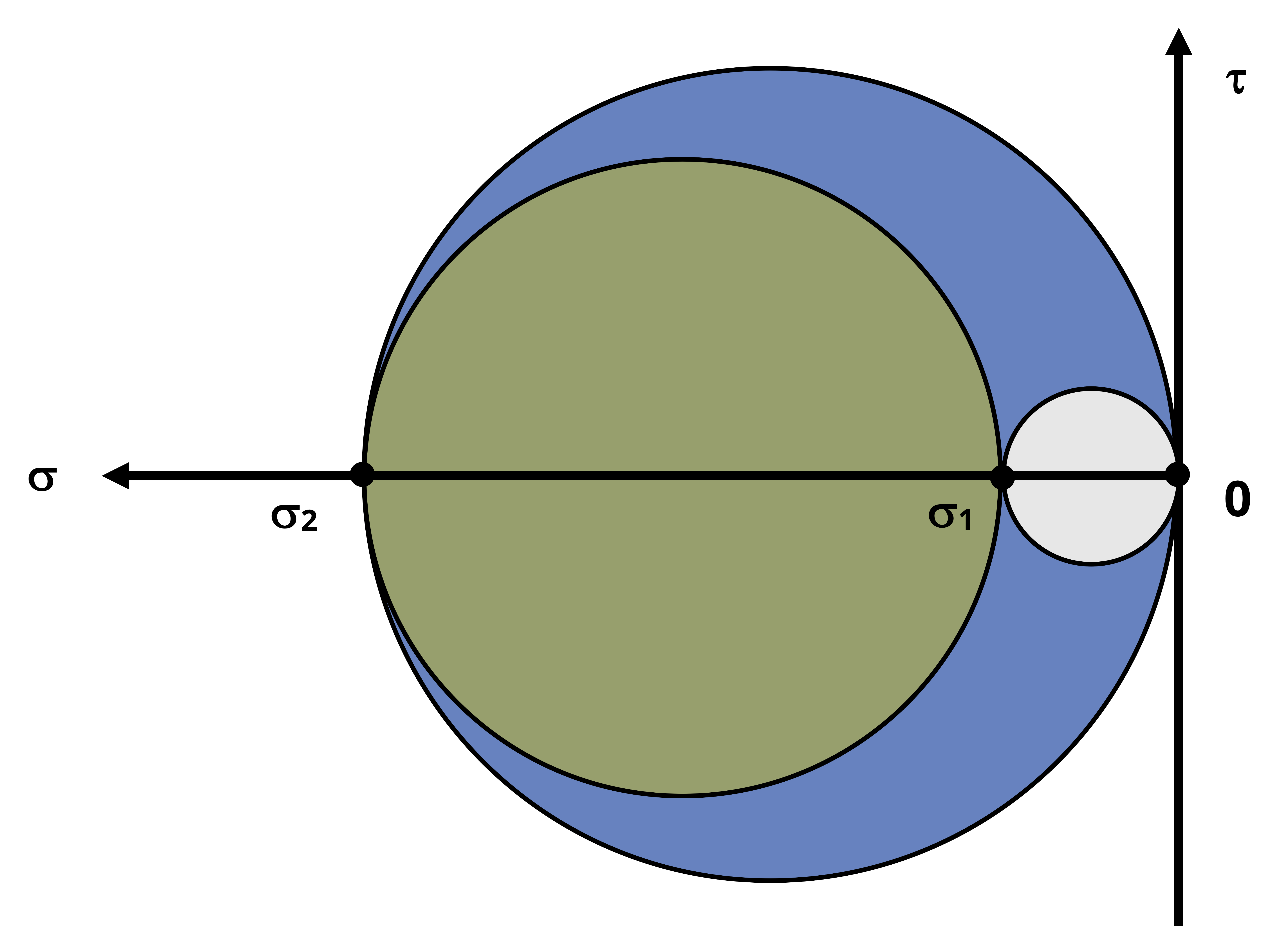
Case 3:
Referring to Figure 12.20, this case is different than the other two because in this case, the Mohr’s circle for the xy plane is the largest circle. This means that the absolute max shear stress and the maximum in-plane shear stress are the same.
So in the case that σ1 and σ2 are opposite in sign, the absolute max shear stress is:
\[ \tau_{(\max )absolute}=\left|\frac{\sigma_1-\sigma_2}{2}\right| \]
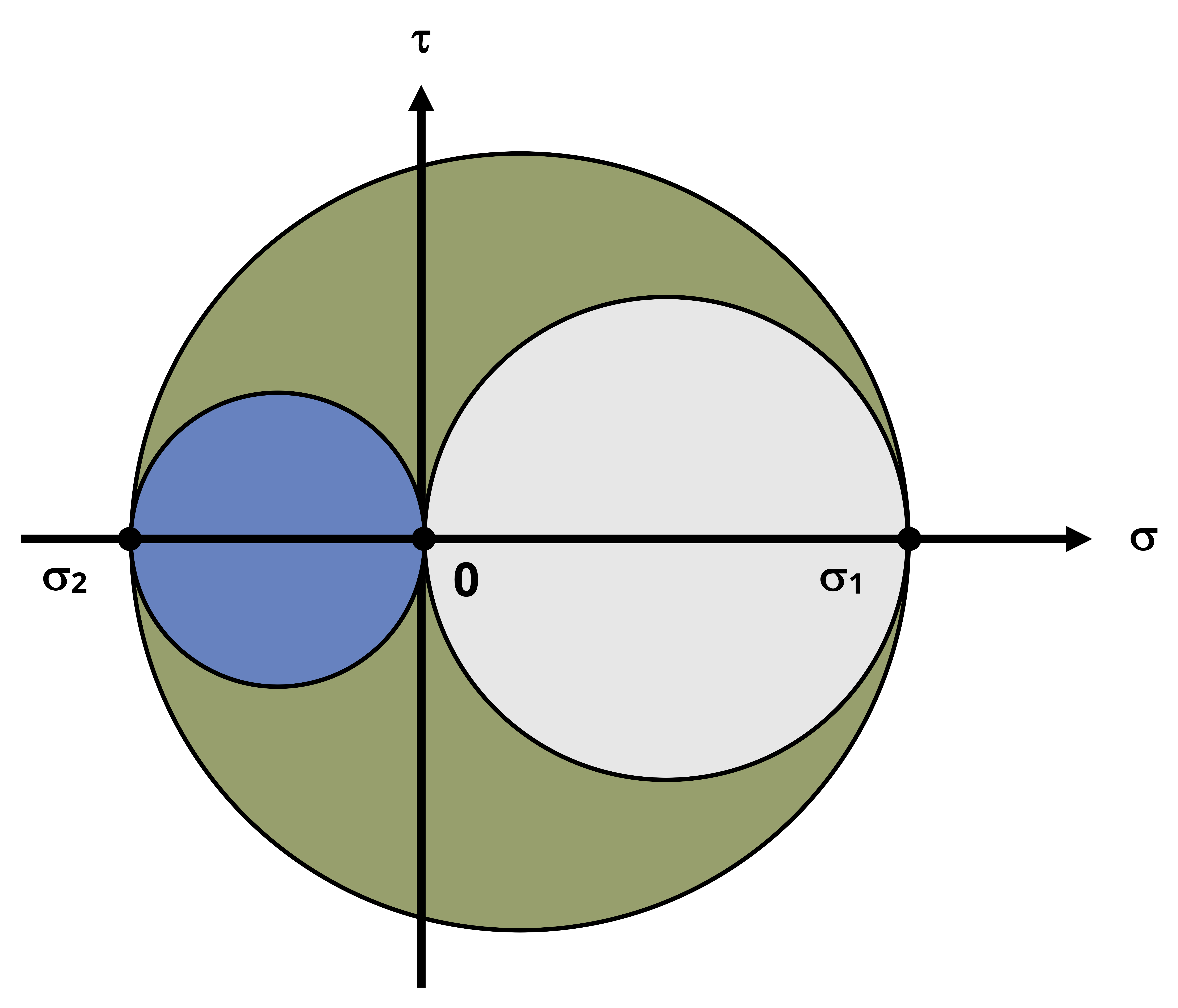
More generally, given principal stresses σ1, σ2, and σ3 = 0, the absolute maximum shear stress can be determined from:
\[ \boxed{\tau_{(\max)absolute}=\left|\frac{\sigma_{\max }-\sigma_{\min }}{2}\right|} \tag{12.6}\]
𝜏(max)absolute = Absolute maximum shear stress [Pa, psi]
𝜎max = Maximum principal stress [Pa, psi]
𝜎min = Minimum principal stress [Pa, psi]
This works for any of the cases above:
Case 1: σmax = σ1, σmin = 0
Case 2: σmax = 0, σmin = σ2
Case 3: σmax = σ1, σmin = σ2
Summary
Click to expand
References
Click to expand
Figures
All figures in this chapter were created by Kindred Grey in 2025 and released under a CC BY-NC-SA license, except for:
- Figure 12.1: A pressurized duct is fabricated with welding in a helical pattern. Sneha Davison. 2024. CC BY-NC-SA.